Lead time refers to the amount of time required for an item or service to be produced and delivered to the customer
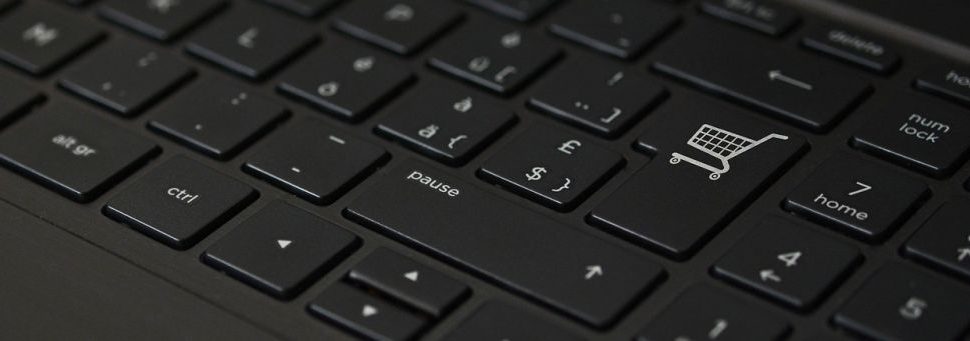
It is a crucial aspect of any business operation, as it directly affects customer satisfaction, inventory management, and overall efficiency. In this article, we will delve into the concept of lead time, its significance, and how it has evolved over time.
The Importance of Lead Time in Business Operations
Lead time plays a critical role in ensuring smooth operations and meeting customer expectations. It encompasses various stages, including the procurement of raw materials, manufacturing or production processes, quality control, packaging, and transportation. Understanding lead time is vital for individuals and businesses involved in supply chain management, production planning, and customer service.
Defining Lead Time
Lead time is the duration between placing an order and receiving the final product or service. It includes every step involved in the production and delivery process, from start to finish. The lead time period may vary depending on the complexity of the product, availability of raw materials, production capacity, and shipping logistics.
Factors Affecting Lead Time
Several factors influence lead time, and understanding them is vital for effectively managing it. These factors include:
– Supply chain management: The efficiency of the supply chain affects lead time significantly. Streamlining processes, building strong relationships with suppliers, and ensuring timely delivery of raw materials are crucial.
– Production capacity: The capacity of the manufacturing facility directly impacts lead time. Higher production capacity allows for quicker order fulfillment, reducing lead time.
– Raw material availability: The availability and reliability of raw materials are essential for maintaining consistent lead times. Supplier relationships and strategic sourcing play a vital role in this aspect.
– Transportation and logistics: Efficient logistics and reliable transportation networks are crucial for timely delivery. Collaborating with reputable logistics partners can help minimize lead time.
– Quality control: Proper quality control measures are necessary during the production process to ensure timely delivery of defect-free products. Identifying and rectifying any issues promptly avoids delays.
Historical Evolution of Lead Time
Lead time has undergone significant changes over the years, driven by advancements in technology, globalization, and shifting customer expectations. Let’s take a closer look at how lead time has evolved:
1. Pre-Industrial Revolution: Lead times were relatively long, often spanning months, as production processes were manual, and transportation methods were limited.
2. Industrial Revolution: The introduction of machinery and mass production techniques led to reduced lead times. Standardized processes and increased production capacities improved efficiency.
3. 20th Century: Technological advancements, such as automation and assembly lines, further reduced lead times. Improved transportation networks and communication systems also contributed to shorter lead times.
4. Globalization: With the rise of international trade, lead time became an even more crucial aspect for businesses. Companies had to consider not only the production process but also the time required for transportation across borders.
5. Digitalization and E-commerce: The advent of the internet and e-commerce revolutionized lead time. Online platforms enabled faster order processing, real-time inventory management, and improved coordination between suppliers and customers. Lead times were significantly reduced, as customers could receive products in a matter of days.
Best Practices for Managing Lead Time
Efficient management of lead time can give businesses a competitive edge. Here are some best practices to consider:
– Predictive Analytics: Utilize data analysis and predictive modeling to forecast demand patterns, enabling better lead time management.
– Strategic Inventory Management: Maintain optimal inventory levels without excessive stockpiling or stockouts. Implement systems such as Just-in-Time (JIT) to minimize lead time and maximize efficiency.
– Collaboration with Suppliers: Build strong relationships with suppliers, ensuring timely delivery of raw materials. Collaborative planning and communication can reduce lead times significantly.
– Continuous Improvement: Continuously evaluate and optimize processes, identifying and addressing bottlenecks and inefficiencies. Utilize lean manufacturing principles to streamline operations.
– Technology Integration: Invest in software and systems that facilitate real-time tracking of orders, inventory, and production processes. Automation and integration can save time and enhance overall efficiency.
In conclusion, lead time plays a vital role in the success of any business. It affects customer satisfaction, inventory management, and overall efficiency. By understanding the factors influencing lead time, businesses can effectively manage it and stay competitive in today’s dynamic market. Embracing technological advancements and implementing best practices allows for shorter lead times, ultimately delivering enhanced customer experiences and increased profitability.